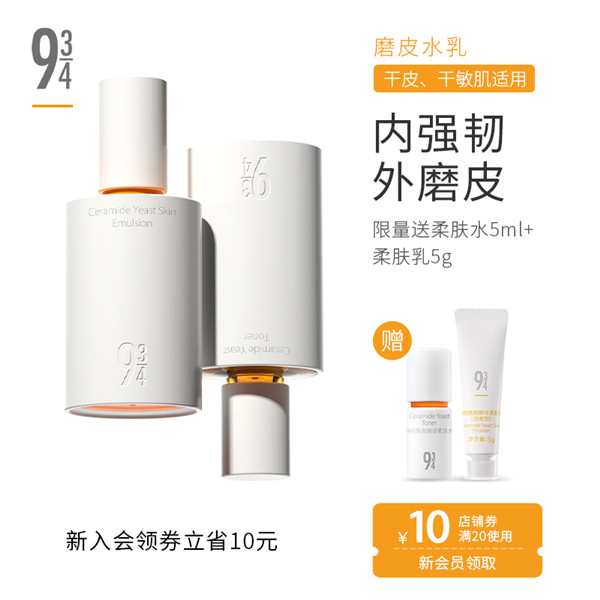
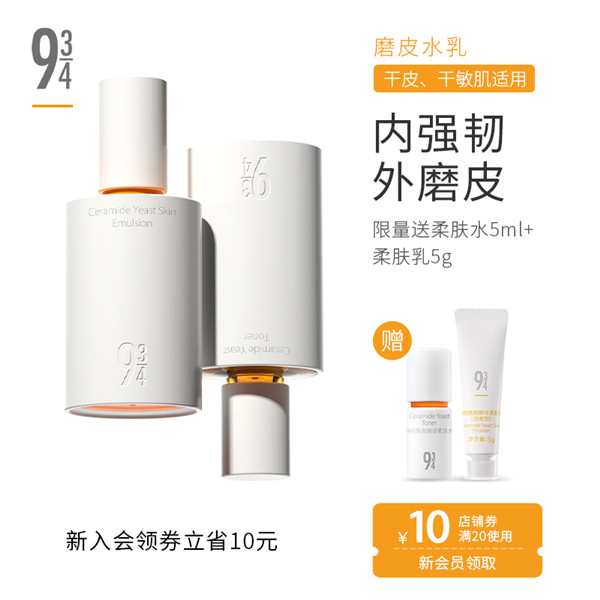
不少人想知道切割工艺优化揭晓!提高效率的7个步骤这些题,以及任务切削条件的话题,想必很多人都想知道,接下来听小编详解。
在现代制造业中,切削技术一直是决定生产效率和产品质量的关键环节之一。本文将深入分析切削工艺优化的关键点,揭示提高生产效率的关键步骤,帮助工程师在激烈的市场竞争中脱颖而出。
选材精准匹配
在优化切割工艺过程中,材料选择是直接影响切割效果和生产效率的重要环节。不同的材料具有独特的物理和化学性能,因此在切削过程中选择材料时必须考虑硬度、耐磨性、导热性和加工性能。
首先,在硬度方面,足够的材料硬度是切削刀具能够穿透工件表面并完成切削过程的先决条件。材料的硬度不仅影响切削力,还与切削刀具的磨损程度直接相关。在实际应用中,综合分析不同硬度材料的性能,可以更好地选择切削加工所需合适硬度的材料。
其次,耐磨性是另一个关键因素。在长期的切削过程中,刀具与工件之间的摩擦和磨损是不可避免的。因此,选择耐磨性能好的材料,可以有效延长刀具寿命,减少刀具更换频率,提高生产效率。
导热性考虑因素也很重要。在高速切削过程中,工件和刀具可能会受到高温的影响。选择导热性能好的材料可以有效散热,减缓温升,保持切割过程的稳定性。
刀具技术的持续改进
在切削技术的演变中,先进的刀具技术已成为提高生产效率和切削质量的关键因素。新一代刀具材料的研发和创新设计使切削过程更加高效、准确和经济。特别是硬质合金、陶瓷刀片、涂层技术等先进材料和工艺的引入,使刀具在面对高速切削和复杂工件时具有更好的表现。
硬质合金刀具以其突出的硬度和耐磨性成为切削行业的明星。优异的耐磨性即使在高速切削条件下也能发挥优异的性能,显着延长刀具寿命。陶瓷刀片以其重量轻、硬度高和化学稳定性而闻名,特别是在加工硬质材料时。应用TiAlN、TiN涂层等涂层技术,不仅提高了刀具的耐磨性,而且减少了摩擦,使切削过程更加顺畅、更加高效。
切削刀具的设计也在不断创新。复合刀具、可调刀具和多刃设计都旨在提供更灵活的切割解决方案。通过合理的几何形状和刃口设计,刀具能够更好地适应不同材料和切削条件,提高加工效率。
科学调整切削参数
在优化切削工艺过程中,合理调整切削参数是提高生产效率和产品质量的关键环节。切削参数如切削速度、进给量、切深等直接影响加工过程中的热、力、振动等因素,因此它们的调整不仅关系到而且直接影响工件的表面质量。影响刀具寿命和整体切削效率。
首先,切削速度的选择是一个关键考虑因素。切削速度太高会增加刀具磨损,而切削速度太低会降低生产率。通过深入分析材料特性、工件要求、刀具性能确定合适的切削速度是提高切削效率的第一步。
其次,合理调整进给速度也很重要。适当的进给速度可以及时清除切削过程中的切屑,减少切削热集中的面积,从而提高刀具的寿命。同时,进给速度的优化与表面质量和加工精度直接相关。
最后,切削深度的选择必须综合考虑刀具和工件的特性。切削深度过深会对刀具造成过大的应力,影响刀具寿命和切削质量。适当的切割深度可以平衡切割效率和切割质量之间的关系。
数控切割系统的优点
数控切割系统的新技术在现代制造中发挥着关键作用,赋予切割工艺前所未有的灵活性和效率。数字控制可以实时监控和调整切削过程,确保每个刀具的运动精确到微米级,提高加工质量,降低废品率并降低生产成本。
除了精度之外,数控切割系统还提供了极大的灵活性。虽然传统切割设备通常需要在每次操作之间进行繁琐的设置和调整,但CNC系统允许通过预编程更轻松地调整切割参数。这增加了生产线的灵活性和适应性,使生产线能够更轻松地适应不同的产品要求并快速切换生产操作。
自动化是数控切割系统的另一个特点。系统自动执行刀具更换、切削深度调整等一系列切削操作,减轻了人工工作负担,提高了生产效率。人机协作的本质意味着操作员可以更加专注于监控和优化切割过程,更好地利用他们的技能和经验。
实时监控与反馈系统
在现代切割过程中,实时监控和反馈系统发挥着重要作用,为生产过程引入了前所未有的智能和灵活性。该系统利用先进的传感器技术,即时捕捉切削过程中从刀具状况到工件表面质量的关键数据,从而实现对生产环境的全面监控。
重要的是,这些系统不仅仅是被动的数据收集器,而是主动的、智能的决策者。当检测到异常情况或潜在题时,系统快速响应,自动调整切割参数,确保生产过程顺利进行。这种实时反馈机制不仅提高了生产效率,还降低了废品率,为公司带来了显着的经济效益。
更有趣的是,随着人工智能技术的发展,实时监控和反馈系统越来越多地自我学习和优化。系统根据历史数据和实际反馈不断调整算法,可以适应不同工件和材料的加工特性,进一步提高工艺的智能化水平。
因此,实时监控和反馈系统是优化切割过程的重要步骤。通过集成该系统,企业可以在激烈的市场竞争中脱颖而出,实现简洁、智能的切割流程,为切割行业的未来发展奠定坚实的基础。
始终强调人机协作。
随着科学技术的快速发展,在切割过程中应用人机协作正成为提高生产效率和质量的重要因素。传统的切割工艺通常依赖于操作员的经验和技能,但人机协作的引入将我们的工作方式提升到了一个全新的水平。
在人机协作系统中,智能机器学习算法与先进的数控技术相结合,使切割过程更加智能、精准、高效。通过与智能系统的紧密配合,操作员可以更好地监控和调整切割参数,快速适应生产变化,并及时响应潜在题。
这种协作方式不仅提高了切割精度和速度,还减少了人为因素造成的错误。工人可以专注于更复杂和创新的任务,而机器则执行枯燥、重复的任务。这种分工使得切割过程更加灵活,有助于应对市场需求的快速变化。
人机协作系统还可以监控实时数据,以快速发现潜在题并进行预测性维护,以减少生产线停机时间。通过不断学习和优化,系统能够逐步适应不同的工艺要求,提高整体生产效率,为企业创造更多的商业价值。
学习成功案例
不要忘记学习,尤其是从成功的例子中学习。这样可以帮助团队积累经验,了解在类似情况下哪些切削参数和工艺设计是有效的,成功案例的实践经验成为团队成员工作的宝贵参考。
通过学习成功案例,您的团队可以更快地适应新技术和材料,学习成功经验,并降低试错成本。为了避免您的团队重复其他人的错误,请务必记住,从失败中学习同样重要。通过了解失败案例的题和挑战,团队可以在优化流程时更好地预防潜在题并提高效率和质量。
对于管理者来说,重要的是组建团队,激发团队凝聚力和创新能力,了解不同行业或领域的成功案例,研究能够以新的思路和灵感推动切削工艺创新和发展的成功案例,我们需要更多。
立铣刀一次可以刃磨的标准长度通常由刀具制造商提供。标准长度可能会因工具型号和制造工艺而异。一般立铣刀的标准磨削长度为3-5mm,但具体磨削长度还应考虑以下因素
加工操作不同的加工操作会导致不同程度的刀具磨损。例如,加工硬质材料会导致刀具磨损更快。
刀具材料不同的刀具材料具有不同的耐磨性,因此标准磨削长度也不同。
刀具直径较大的刀具直径可以承受更大的切削力和磨损,从而允许更长的标准重磨长度。
使用立铣刀时,建议根据加工操作和刀具制造商的建议确定合适的磨削长度。一旦刀具出现一定程度的磨损,必须及时修复,以保证加工质量和刀具寿命。
CNC切削速度设置取决于多种因素,包括所加工材料的性质、刀具类型、切削条件和工件要求。切削速度一般由两部分组成切削速度和进给速度。
切削速度是指加工时刀具与工件接触的线速度,通常以单位时间内的切削距离来表示,常用单位为米/分钟。切削速度的设定应根据被加工材料的硬度、刀具材料、刀具直径等参数确定。具体切削速度值可参考材料切削速度表或经验公式确定。
进给速度是指加工时工件相对于刀具移动的速度,一般用单位时间内移动的距离来表示,常用单位为mm/min。设置进给速度必须考虑加工精度要求、刀具的切削能力、工件的几何形状等因素。
在实际工作中,需要根据具体情况进行试切和调整。初始设定时,可以选择合理的切削速度和进给量,然后根据加工效果进行调整,以达到理想的加工质量和生产效率。
不同的加工工序可能需要不同的切削参数设置,因此在使用数控机床进行加工时,必须根据具体情况进行调整和优化,以确保加工过程安全、高效、质量可靠。在使用数控机床之前,建议参考制造商提供的相关操作手册和建议,以获得更准确的参数设置和操作说明。
Mastercam2022允许您通过逐步创建来逐步输出程序。
首先选择您需要的项目,从工具栏打开NC程序编写界面,选择“加工指令”菜单,会出现加工指令对话框。
在加工顺序对话框中,可以设置操作类型、刀具形状、原点、切削条件和刀具等信息。
然后点击生成功能键,Mastercam2022就会逐渐生成程序。
创建程序后,可以预览和检查,检查后可以直接打印到机床上进行加工。
逐步创建程序可以让您更好地控制程序流程,避免因一些细节题而导致处理中断。
评论已关闭!